(Chemical properties )Stain-resistance test , Solvent stress-cracking resistance , Environmental stress-cracking resistance..........S.S
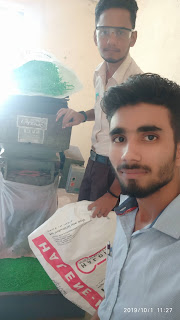
(01) IMMERSION TEST (ASTM D 543, ISO 175) The method of measuring the resistance of plastics to chemical reagents by simple immersion of processed plastic specimens is a standard procedure used throughout the plastics industry. The method can only be used to compare the relative resistance of various plastics to typical chemical reagents. The test results do not provide a direct indication of suitability of a particular plastic for end-use application in certain chemical environments. The limitation infl uencing the results, such as duration of immersion, temperature of the test, and concentration of reagents should be considered when studying the test data. For applications involving continuous immersion, the data obtained in short-time tests are useful only in screening out the most unsuitable materials. The test equipment consists of a precision chemical balance, micrometers, immersion containers, an oven or a constant-temperature bat...